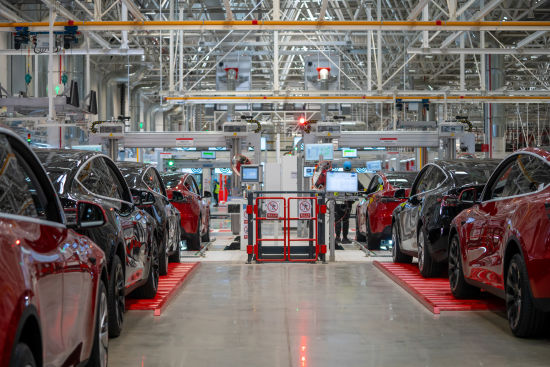
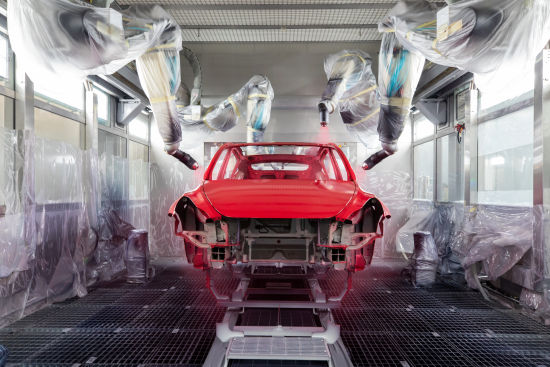
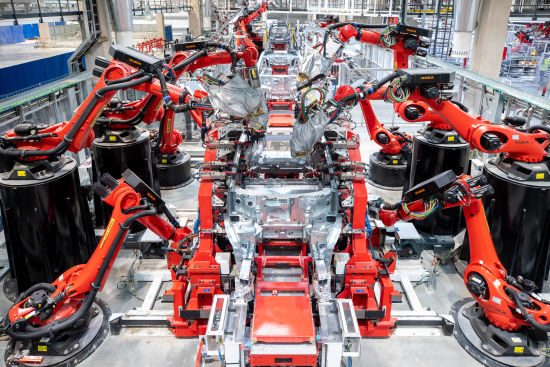
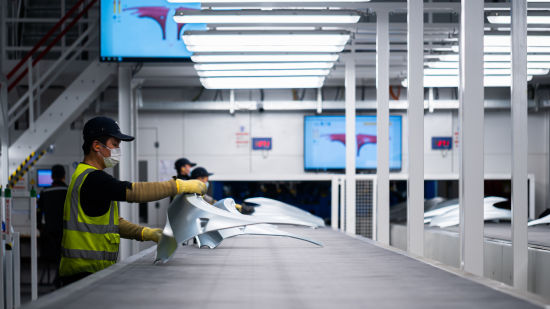
中新网上海新闻9月5日电(李姝徵)近日,多家专业媒体一同探访了特斯拉上海超级工厂,深入了解了其在智能化生产和产品全生命周期质量管理两方面的建设。
特斯拉方面表示,数字化和智能化是特斯拉上海超级工厂的一大特点,冲压、涂装车间产线自动化率更是达到100%。
据特斯拉介绍,“特斯拉速度”与“中国速度”相碰撞,造就了上海超级工厂享誉业界的纪录:从奠基到投产仅花费10个月;2018年当年签约、当年取得土地、当年获取施工许可证;2019年当年开工、当年投产、当年交付。特斯拉上海超级工厂占地面积逾86万平方米,目前在产Model Y和Model 3两款车型。
目前,特斯拉已经完成了将上海超级工厂作为主要汽车出口中心的转型,产量目标已超45万。据介绍,上海超级工厂零部件本地化率高达86%,切实助益中国新能源汽车上下游产业链的成长。与此同时,车辆出口欧洲、日本、东南亚等超过10个国家和地区,将中国制造推送到世界舞台。
“数字神经网”布及产线的每个角落
早前,中国信息通信研究院院长余晓晖曾指出:“工业互联网是数字化转型的路径和方法论,这是构建物理世界的框架模式。”通过对人、机、物的全面互联,构建起全要素、全产业链、全价值链全面连接的新型生产制造和服务体系,工业互联网是数字化转型的实现途径,能有效变革生产制造模式。
上海超级工厂的数字化、智能化其犹如“科技电影世界”。特斯拉自主研发了生产制造控制系统(MOS),具备人机交互、智能识别及追溯功能,深入支持世界顶级的制造工艺。
据刘经理介绍,MOS系统深度应用于整车制造、电池车间、电机车间等,有效提升工艺、工程设计、质量控制等。
除了MOS系统,在上海超级工厂,高可靠性的工业网络覆盖自动化生产线的各个角落,为设备自动化、生产设备无线联接、生产信息数据采集、人机交互、智能化决策等提供完善的网络服务。通俗来说就是既保证产品生产过程的标准化,确保产品质量,又能利用大数据系统回溯每台车、每个零部件的生产数据。
以这次参观的压铸车间为例。压铸车间利用特斯拉自主开发的大数据分析系统,对压铸工艺参数实现全面的数据统计,并进行参数波动报警功能,确保从源头控制零部件的品质稳定可控。同时通过仪器扫描对产品进行质量监控,通过MOS系统对产品批号和可追溯性进行全方位管理。
产品全生命周期质量管控 “抽丝剥茧”保质量
备受关注的还有特斯拉产品全生命周期质量管控。从供应商端到零部件检验,再到制造过程,最后到顾客使用,上海超级工厂会对每一辆车实施全生命周期的质量管控。
整个质量管控由3大基本面共同支撑:
首先,数字化、智能化的生产制造控制系统在产品质量精细化管理方面发挥了重要作用,它实现数据采集和精确追溯等功能。其中数据采集系统实现了从细节到整体的全方位数据收集,不仅达到全尺寸监控和管理,还实现了整车工厂与全供应链零件尺寸检测数据的实时采集。同时支持自动进行大数据分析,对尺寸偏差进行预判;精确追溯系统则会对关键工位安装及过程参数监控全记录,支持追溯生产过程数据查询和分析。
而在生产制造过程中特斯拉设置了细致又严苛的质量检测环节。生产过程中会针对车身尺寸进行标准化控制,多种检测检具与自主开发的测量数据分析系统相结合,发现变异及时报警;同时整车固件电器功能可以实现281项自动检测,配合人工检测确保功能正常。值得一提的是,针对电池、电机等关键零部件,特斯拉采用近50套自动检测设备进行检测,确保气密、高压绝缘、电性能、电机焊接质量等符合标准,并且所有测试数据上传到数据库长期可追溯。
此外,特斯拉还设立了Audit评审这一人工检验方式。Audit评审是由经过专业训练的评审员独立地站在用户使用产品的立场上,以专业、全面的眼光,对已确认合格的整车进行随机抽样质量评价,确保每台车都达到质量要求。特斯拉相信,完全从用户角度出发审视产品,更能发现问题并改进问题。
车辆下线并非质量管理的终点。车辆下线后,售后质量管理开始“接管”。从车辆下线出厂开始,从物流运输环节、交车前检查环节、交付后客户使用环节,全面呵护车辆的质量表现和客户的用车感受,快速响应市场反馈,高效解决客户需求。正是这“抽丝剥茧”的质量管理体系,实现了全过程质量数字化监控、智能化分析和预防工作。(完)
注:请在转载文章内容时务必注明出处!
编辑:李姝徵